工业上一般采用的线速是入口处为4-7m/s ,出口处为12-18m/s。随着反应深度的增大,油气体积流量增大,因此有的提升管反应器由不同直径的两段(上粗下细)组成二提升管反应器的高度由反应所需时间确定,工业设计时多采用2-4s的反应时间。
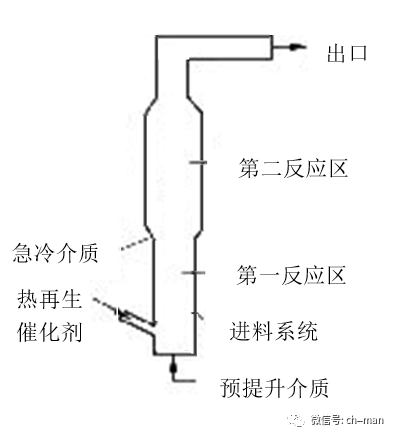
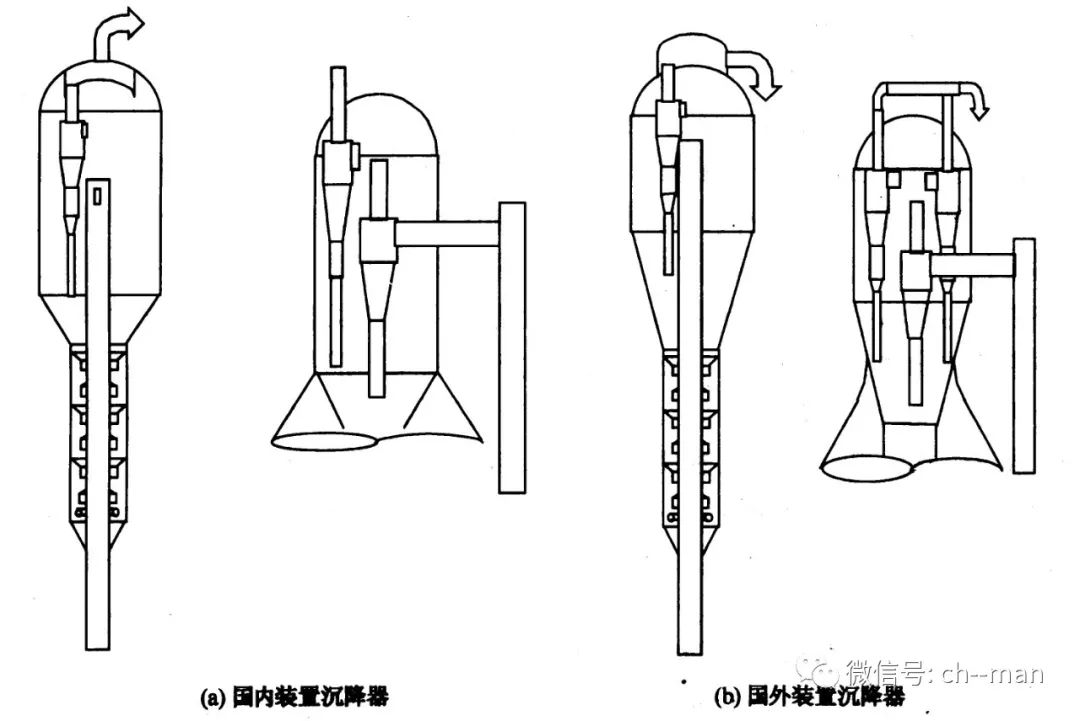
再生器是催化裂化装置的重要工艺设备,其作用是为催化剂再生提供场所和条件。它的结构形式和操作状况直接影响烧焦能力和催化剂损耗。再生器是决定整个装置处理能力的关键设备。
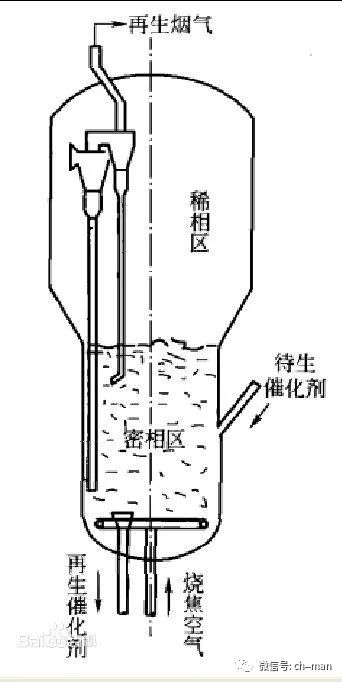
再生器筒体是由A3碳钢焊接而成的,由于经常处于高温和受催化剂颗粒冲刷,因此筒体内壁敷设一层隔热、耐磨衬里以保护设备材质。筒体上部为稀相段,下部为密相段,中间变径处通常叫过渡段。
密相段是待生催化剂进行流化和再生反应的主要场所。在空气(主风)的作用下,待生催化剂在这里形成密相流化床层,密相床层气体线速度一般为0.6~1.0m/s,采用较低气速叫低速床,采用较高气速称为高速床。密相段直径大小通常由烧焦所能产生的湿烟气量和气体线速度确定。密相段高度一般由催化剂藏量和密相段催化剂密度确定,一般为6~7m。
稀相段实际上是催化剂的沉降段。为使催化剂易于沉降,稀相段气体线速度不能太高,要求不大于0.6~0.7m/s,因此稀相段直径通常大于密相段直径。稀相段高度应由沉降要求和旋风分离器料腿长度要求确定,适宜的稀相段高度是9~11m。
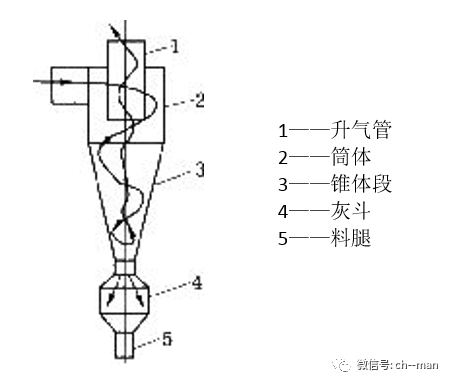
旋风分离器的作用原理都是相同的,携带催化剂颗粒的气流以很高的速度(15~25 m/s)从切线方向进入旋风分离器,并沿内外圆柱筒间的环形通道作旋转运动,使固体颗粒产生离心力,造成气固分离的条件,颗粒沿锥体下转进入灰斗,气体从内圆柱筒排出。灰斗、料腿和翼阀都是旋风分离器的组成部分。灰斗的作用是脱气,即防止气体被催化剂带入料腿;料腿的作用回收的催化剂输送回床层,为此,料腿内催化剂应具有一定的料面高度以保证催化剂顺利下流,这也就是要求一定料腿长度的原因;翼阀的作用是密封,即允许催化剂流出而阻止气体倒窜。
主风分布管是再生器的空气分配器,作用是使进入再生器的空气均匀分布,防止气流趋向中心部位,以形成良好的流化状态,保证气固均匀接触,强化再生反应。
辅助燃烧室是一个特殊形式的加热炉,没在再生器下面(可与再生器连为一体,也可分开设置),其作用是开工时用以加热主风使再生器升温,紧急停工时维持一定的降温速度,正常生产时辅助燃烧室只作为主风的通道。
随着分子筛催化剂的使用,对再生催化剂的含炭量提出新的要求,为了充分发挥分子催化剂高活性的特点,需要强化再生过程以降低再剂含炭量,近年来各厂多采用CO助燃剂,使CO在床层完全燃烧,这样就会使得再生热量超过两器热平衡的需要,发生热量过剩现象,特别是加工重质原料,掺炼或全炼渣油的装置这个问题更显得突出,因此再生器中过剩热的移出便成为实现渣油催化裂化需要解决的关键之一。
再生器的取热方式有内外两种,各有特点。内取热投资少,操作简便,但维修困难,热管破裂只能切断不能抢修,而且对原料品种变化的适应性差,即可调范围小。外取热具有热量可调,操作灵活,维修方便等特点,对发展渣油催化裂化技术具有很大的实际意义。
外取热器是在再生器外部设置催化剂流化床,取热管浸没在床层中,按催化剂的移动方向外取热器又分为上流式和下流式两种。
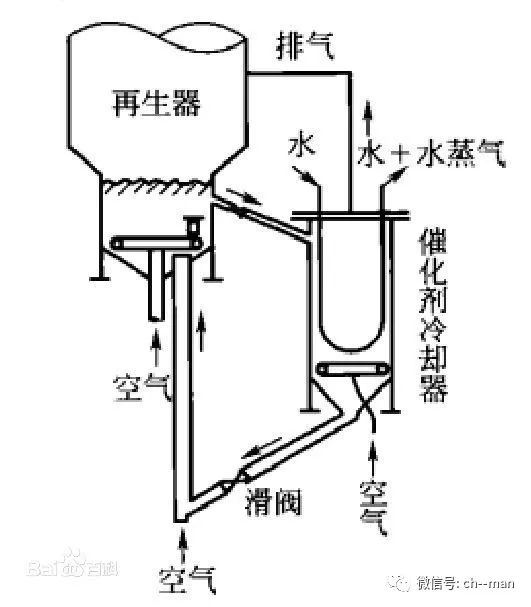
国内首先使用的是牡丹江炼油厂的催化裂化装置,效果良好。它是将再生器密相床上部或二密(烧焦罐式再生器)700℃左右的高温再生催化剂引出一部分进入取热器,使其在取热器列管间隙中自上而下流动,列管内走水。在取热器内进行热量交换,在取热器底部通入适量空气,维持催化剂很好地流化,通过换热后的催化剂温降一般约为100~150℃,然后通过斜管返回再生器下部(或烧焦罐的预混合管)。
催化剂的循环量根据两器热平衡的需要由斜管上的滑阀控制,气体自取热器顶部出来返回再生器密相段(或烧焦罐)。由于下流式外取热器的催化剂颗粒与气体的流动方向相反所以其表观速度均较小,因之对管束的磨损很小,而且床层的温度均匀。试验证明床内各处温度几乎相同,通过对管壁温度的计算和分析认为在正常情况下管外壁温度约为243℃最高也只有278℃左右,因此可以采用碳素钢管(取热器支撑件需用合金钢)。这种取热器的布置与高效烧焦罐式再生器及常规再生器均能配套,通入少量空气就能维持外取热器床层良好的流化状态,动力消耗小,特别是对老装置改造更为适宜。
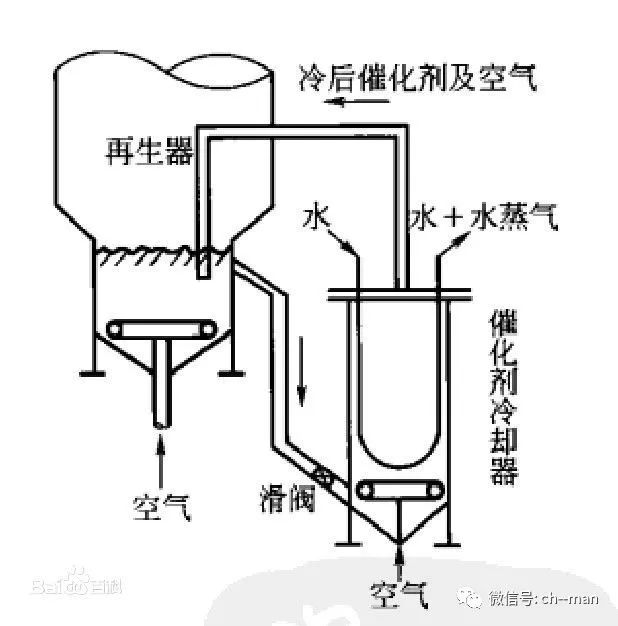
这种型式的取热设备国内于1985年分别在九江及洛阳炼油厂催化裂化装置上使用。它是将部分700℃左右的高温再生催化剂自再生器密相床底部引出,再由外取热器下部送入。取热器底部用增压风使其沿列管间隙自下而上流动,应注意催化剂入口管线避免水平布置,并要通入适量松动空气以适应高堆比催化剂输送的要求。气体在管间的流速为1.0~1.6m/s,列管无严重磨损,催化剂与气体一起自外取热器顶部流出返回再生器密相床。催化剂循环量由滑阀调节。水在管内循环受热后部分汽化进入汽包,水汽分离得到饱和汽。取热用水需经软化除去抽盐分或用回收的冷凝水。
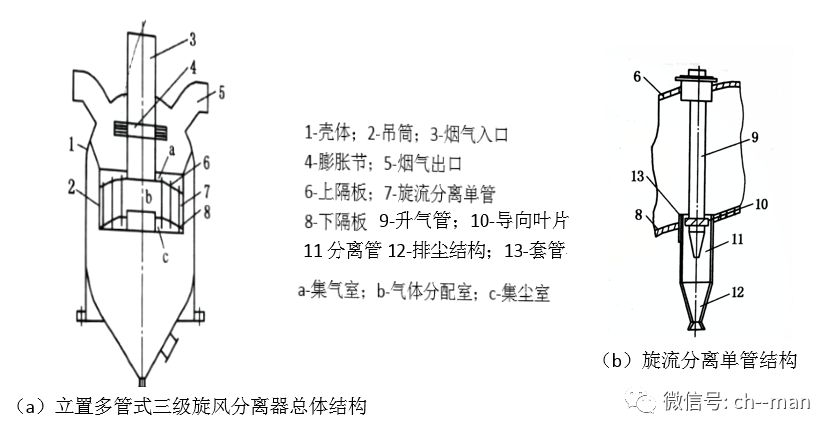
催化裂化装置高温再生烟气的能量回收系统是一项重要节能措施,近几年来发展很快。第三级旋风分离器是该系统的重要设备之一。它的性能好坏直接关系到烟机的运行寿命与效率。目前国内催化裂化装置采用的三旋有多管式、旋流式、布埃尔式,国外还开发出水平多管式,分离效率更高。多管三旋是由分离器壳体内装有数十根旋风管并联组成的旋风分离器其主要元件是旋风管,旋风管主要由导向器、升气管排气锥、泄料盘和旋风筒四部分组成
单动滑阀用于床层反应器催化裂化和高低并列式提升管催化裂化装置。对提升管催化裂化装置,单动滑阀安装在两根输送催化剂的斜管上,其作用是:正常操作时用来调节催化剂在两器间的循环量,出现重大事故时用以切断再生器与反应沉降器之间的联系,以防造成更大事故。运转中,滑阀的正常开度为40~60%。
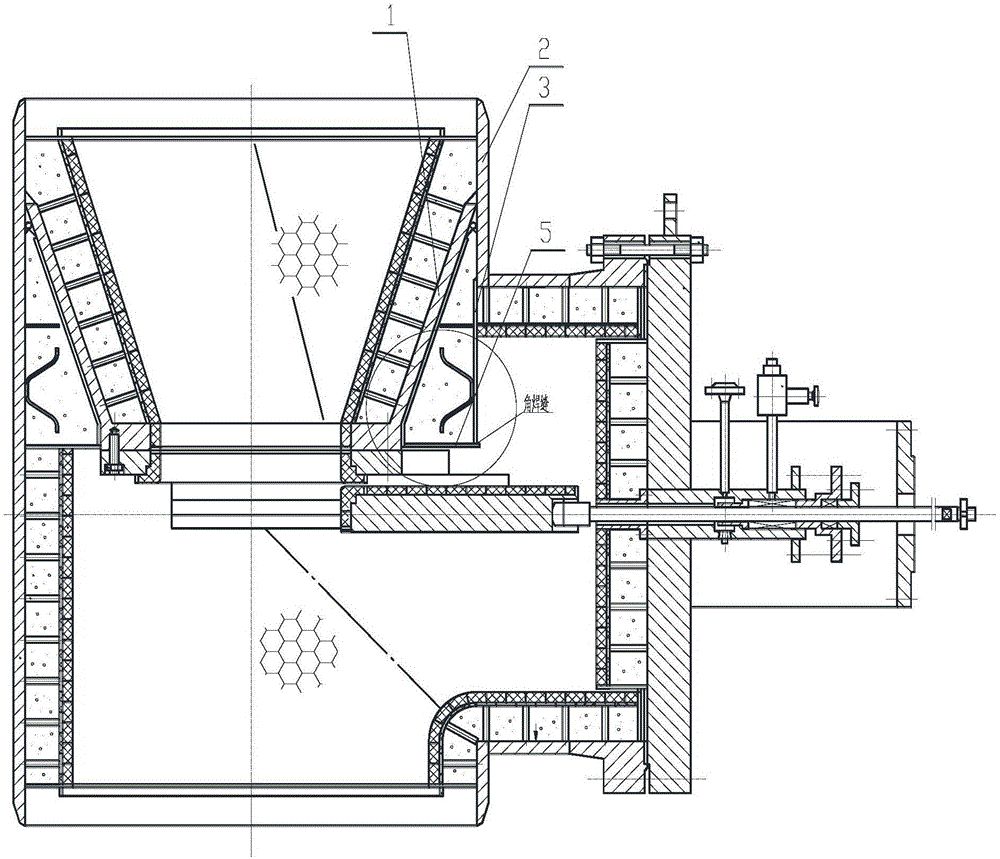
双动滑阀是一种两块阀板双向动作的超灵敏调节阀,安装在再生器出口管线上(烟囱),其作用是调节再生器的压力,使之与反应沉降器保持一定的压差。设计滑阀时,两块阀板都留一缺口,即使滑阀全关时,中心仍有一定大小的通道,这样可避免再生器超压。
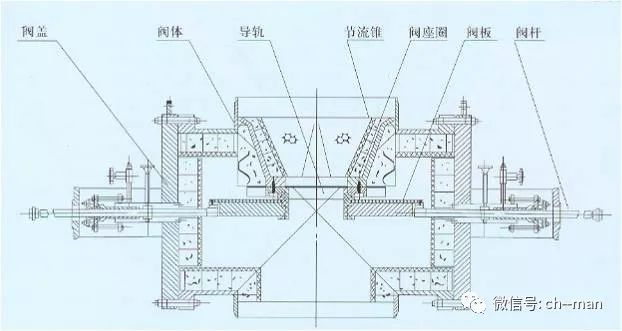
在同轴式催化裂化装置利用塞阀调节催化剂的循环量。塞阀比滑阀具有以下优点:
③安装位置较低,操作维修方便。在同轴式催化裂化装置中塞阀有待生管塞阀和再生管塞阀两种,它们的阀体结构和自动控制部分完全相同,但阀体部分连接部位及尺寸略有不同。结构主要由阀体部分、传动部分、定位及阀位变送部分和补偿弹簧箱组成。
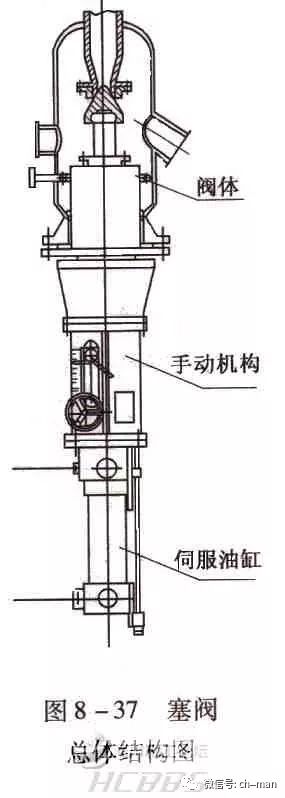
烟气能量回收设备主要包括主风机、增压机、高温取热器(一、二再烟气混合后)、烟气轮机以及余热锅炉等,其主要任务:
①为再生器提供烧焦用的空气及催化剂输送提升用的增压风、流化风等;
主风机:主风机是把旋转的机械能转换为空气压力能和动能,并将空气输送出去的机械。在催化裂化装置中主风机主要有以下几方面作用:催化剂再生烧焦供氧;两器流化供风;烘干再生器和沉降器衬里;为增压机提供风源。目前我国各炼油厂的催化裂化装置所用的主风机分为离心式和轴流式两种,其压力在0.2~0.4MPa之间,它们都是叶片旋转式机械。现分述如下:1.离心式主风机2.轴流式主风机
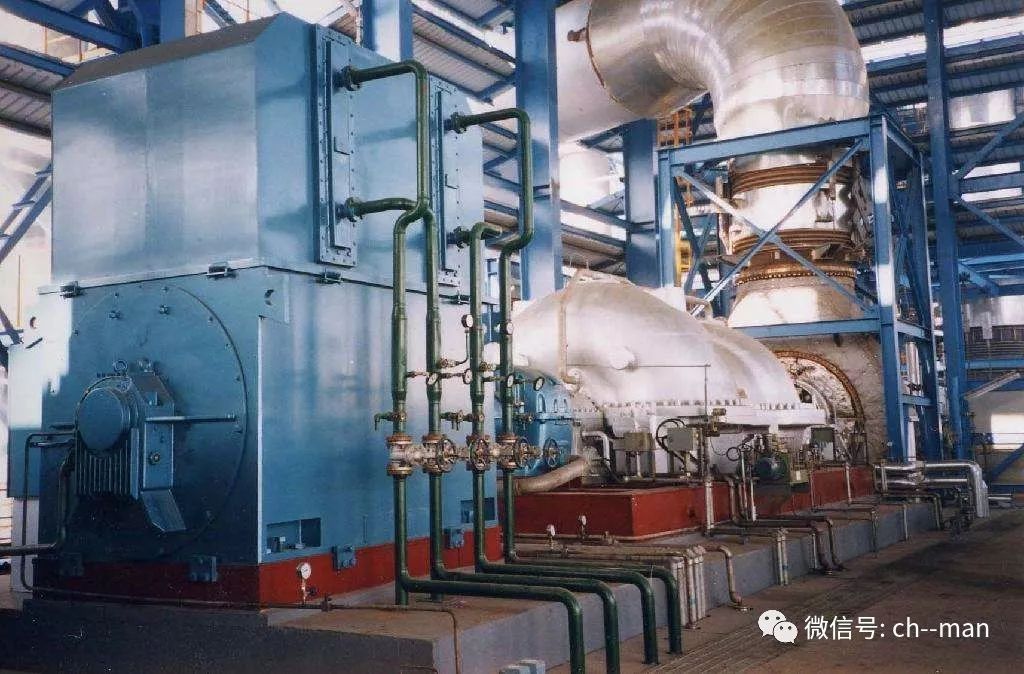
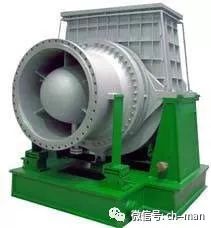
烟气轮机的结构(以双级烟气轮机为例)由导流锥、一级静叶、一级动叶、二级静叶、二级动叶、轴、机壳、蜂窝密封、出口过渡段、梳齿密封等组成。
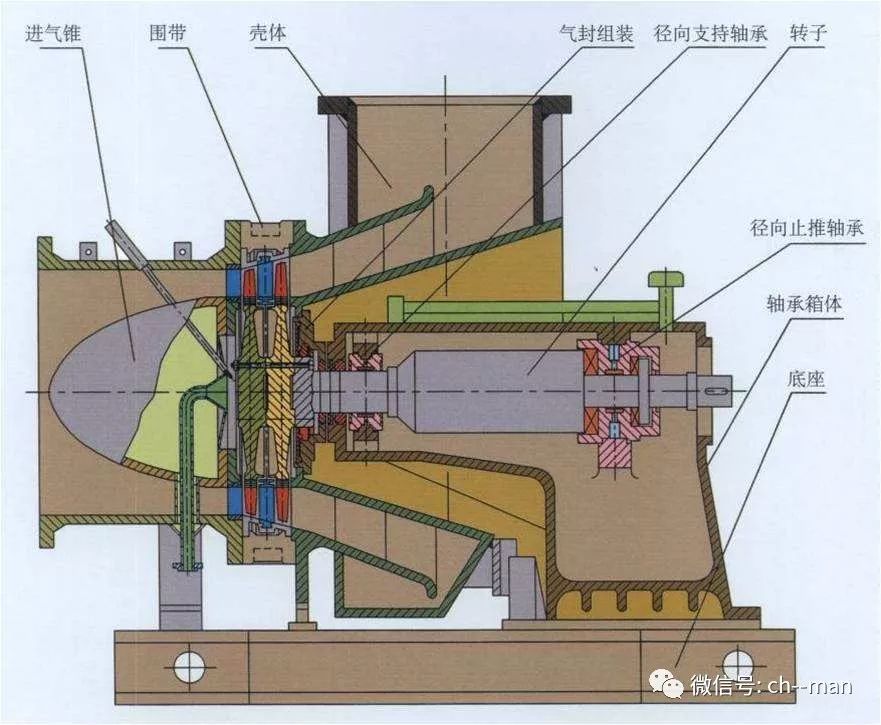
烟气轮机实质上是将压力能和热能转化为电能或机械能的机械,以具有一定压力的高温烟气推动烟机旋转,进而带动主风机和发电机做功,实现能量回收。在烟机能量回收机组中,烟机是关键设备,它直接影响着能量回收的经济效益。目前我国催化装置上采用的有单级悬臂式烟机、双级悬臂式烟机和多级双支承式烟机。因高温烟气中含有催化剂固体微粒,以高速度冲蚀磨损着烟机的叶片,所以要求烟机选用耐高温、耐冲蚀、耐磨损的高合金材料,采用合理的设计结构,尽可能地延长使用寿命。烟气轮机利用压力能和热能实现能量回收有多种方式:直接发电、带动主风机、带动主风机并发电。
当含有固体微粒的烟气流过叶片时,对叶片的冲蚀程度与烟气中固体微粒的粒度、浓度、通流部分的空气动力性质以及叶片表面的耐磨性能有关。烟气中携带的催化剂微粒以高速和烟机内件相撞击,发生机械作用。叶片是受冲蚀、磨损最严重的部件,烟机的速度越高对叶片的冲蚀速度就越快,烟机的寿命越短。而烟机的使用寿命直接影响到能量回收的经济效益。影响烟机叶片寿命的主要因素是:
设计上采用耐磨材料和防冲蚀措施。为了减少烟气中微粒的冲蚀作用,流道必须设计成能防止微粒局部集中的。烟机轮机设计成多级,烟气流速大约可能低至单级烟机的1/2,催化剂微粒的动能约减少到1/4,即减少了催化剂微粒在叶片内弧上的冲击力;催化剂微粒的冲蚀效应与动能成正比,即与气流速度的平方成正比。因此气流速度的降低可使叶片的使用寿命增加。
其次,多级烟机的设计,带来了相对较低的气动级负荷,在静叶和动叶的流道中具有较小的转折角,相应地减少了在叶栅转折过程中作用到催化剂微粒上的离心力,因此减缓了在动叶内弧从进气到出气边的冲蚀效应。沿叶高的冲蚀效应不是均匀分布的,在具有性质不同的二次流图形的各个面积处更为明显。为了防止在叶根部分局部催化剂微粒的集中,在每一叶排前设置耐冲蚀的转折台阶,当气流中催化剂微粒随气流靠近边壁时,转折台阶使之转折至流道的中部,于是减少了流道边壁处的催化剂集中。这就消除了通过冲蚀叶片根部截面发生折断动叶片的危险。转折台阶表面堆焊硬质合金或爆炸喷漆涂碳化铬,提高其耐冲蚀能力。增大各排叶片的轴间距离,能使沿叶高催化剂微粒达到均匀分布。烟机静叶和动叶的轴间距离增加到燃气轮机相应距离的1.5倍。
经验表明,叶片出气边的冲蚀效应甚为明显,对动叶尤为突出。为了增加叶片的使用寿命,将叶片出气厚度大约增加到燃气轮机叶片的2倍。延长烟机的寿命,除在烟机本身采用耐冲蚀措施外,还需要采用高效率的一、二、三、四级旋风分离器,使进入烟机中烟气含气尘量减少。操作方面控制减少烟气中催化剂粉尘含量虽然烟机采用了耐冲蚀措施,系统中也采用了高效率的旋风分离器,但是单纯靠烟机和旋风分离器还不够,还必须严格控制平稳操作,减少因操作波动而引起的催化剂大量跑损。因而要保持装置在合理的条件下平稳操作,降低催化剂跑损(单耗),是延期烟机和三旋寿命,提高能量回收系统经济效益的重要因素。
余热锅炉用于回收烟气中热量产生饱和蒸汽。经过烟机后的一、二再烟气,进入余热锅炉的蒸发段,对饱和蒸汽进行加热,产生过热蒸汽。加热饱和蒸汽后的烟气依次经过蒸发段、省煤器然后由烟囱排出。余热锅炉的蒸发段是余热锅炉产生饱和蒸汽的场所。余热锅炉的省煤器是利用烟气的余热加热锅炉给水温度的场所。
本篇文章来源于微信公众号: 催化人
声明:本站所有文章,如无特殊说明或标注。任何个人或组织,在未征得本站同意时,禁止复制、盗用、采集、发布本站内容到任何网站、书籍等各类媒体平台。如若本站内容侵犯了原著者的合法权益,可联系我们进行处理。